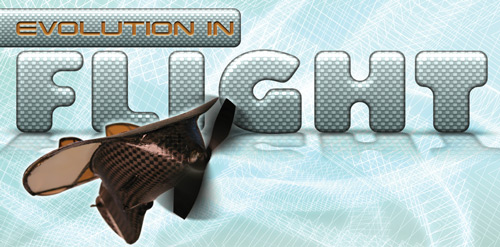
Micro Air Vehicles have grown progressively smaller and smarter
By Aaron Hoover
downloadable pdf
Israeli army soldier Raphael Haftka was on a patrol near the Jordanian border in 1962 when the hiss of bullets forced him to take cover. Shaken but uninjured, he was aghast to learn the shooters were fellow Israelis who mistook him for the enemy.
That incident occurred when Haftka was 18. But he never forgot it as he pursued a career in aerospace engineering on a path that eventually brought him to the University of Florida as a professor. When the arrival of a new department chairman prompted faculty to brainstorm new research directions, Haftka hit on tiny surveillance airplanes — planes that ordinary infantry could count on in the heat of battle.
“One of the things I had in mind was a soldier carrying one in his backpack, and then launching it to see who was doing the shooting,” he says.
That was in 1995, a time when small planes were made out of balsawood, paper and gas-fueled engines and strictly the province of hobbyists. With wingspans of two feet or more, the planes were fragile and unreliable. They were also radio-controlled, which meant that only people with the skills of a pilot could fly them. Cute and fun, they were expensive and elaborate toys, not military hardware.
A little more than a decade later, the situation is radically different, thanks to research efforts launched more or less simultaneously by Haftka and a handful of other aerospace engineers at the U.S. Navy and elsewhere. Today, engineering faculty and students at UF and more than a dozen other institutions routinely build what have been named “micro air vehicles,” or MAVs, with wingspans of less than six inches.
Powered by tiny electric motors and equipped with marble-sized video cameras, the UF planes’ balsawood and paper have been supplanted with space-age composites. When not in use, their wings fold up, enabling them to be squeezed into lipstick–sized tubes — and when flying, their wings may flex or pivot up and down for stability and agility. While still remote-controlled, the planes are increasingly capable of remaining aloft and performing missions on their own, a result of innovations in electronics, robotics and software. In the realization of Haftka’s vision, one UF researcher recently designed a plane for U.S. Special Forces to specifications allowing it fit in a uniform pocket. At least two private companies, meanwhile, are manufacturing small surveillance airplanes based on UF research. One has been test-flown in Iraq.
Such rapid development is unusual in university science and engineering research, which is slow and incremental almost by definition. It occurred in part because of the right combination of luck and personalities. But the story behind the success of UF’s micro air vehicle program is also one of experiment, innovation and hard work.
A Thicket of Challenges
Haftka first shopped around his idea at a department Christmas party in 1996. Colleagues and the new chairman, Wei Shyy, were enthusiastic, and they quickly cobbled together a spring graduate class. “The course was mainly to get us all up to speed and to survey the then state-of-the-art,” says Shyy, now chairman of the aerospace engineering department at the University of Michigan.
Shyy persuaded Dave Jenkins, an associate engineer in the department, to teach the class. Jenkins had a talent unique to the department: He was an experienced remote-control airplane hobbyist. About a half dozen students signed up and were assigned different research topics. “We just decided to dig into the area,” Jenkins says.
Researchers quickly realized that they confronted a thicket of challenges. One was the inherent difficulty of making the planes smaller while still keeping them in the air. The shorter the wingspan, the more the plane struggles to overcome aerodynamic drag. A second was the problem posed by wind, with small gusts that would leave larger planes untouched easily sending smaller ones into tailspins. A third was the tiny engines, which were messy and difficult to start. Further down the road lay still more intimidating challenges, such as making the planes easier rather than tougher to fly, which was the natural result of making them smaller.
Most aerospace engineers today use highly computerized design technology, creating virtual models and simulating their performance many times over before building physical prototypes. But at the time — and to some extent even now — no such tools existed for micro air vehicles. So the research was tied more to experiments than simulation, more to practical experience than aerospace theory.
“We kept test-flying them and crashing them,” Jenkins says of the early days. “It was kind of hard-won knowledge.”
Knowing other universities were also struggling to make headway, Haftka organized a competition in hopes of spurring innovation. Five teams turned out for the first International Micro Air Vehicle Competition, held in a field near UF in 1997. UF’s plane, a traditional balsawood model with a two-foot wingspan, completed the mission of flying over and videotaping a target, but the team lost based on design issues.
Undaunted, Jenkins, Haftka and a handful of students continued the work, joined by Peter Ifju, a young aerospace engineering faculty member who was an expert in composite materials. The team started applying for and winning research funding including, by 2000, $500,000 from various funding agencies including NASA, U.S. Special Operations Command and the National Science Foundation.
“I had the remote-control experience and Pete had the composite materials,” Jenkins says. “Rafi was the conceptual guy, and Wei was willing to listen.”
Small and Indestructible
Ifju is an avid and nationally ranked windsurfer who designed and helped build his family’s log home, and he naturally enjoys getting his hands dirty. Early on he recognized a serious flaw with the balsawood models: They were too fragile.
The problem wasn’t that they broke up catastrophically with each crash — and all flights by definition end in crashes, since MAVs have no wheels. It was that crashes chipped or bent the planes’ wings and tails, or altered their rudder and elevator alignments, just enough to throw their sensitive aerodynamics out of whack. That meant improving the planes’ flight characteristics proved a moving target. The researchers would devote two or three flights to “trimming out” the plane to get the elevator and rudder positions just so, only to have a crash throw those surfaces out of balance. The result was a lot of time in the field with few insights as to what designs worked best.
“We realized that in order to get these planes trimmed out properly, you can’t sustain any damage,” Ifju says.
Ifju also recognized that the rigid balsawood surfaces left the planes susceptible to gusts because they had no “give.” Shyy and Jenkins had investigated the possibility of using flexible wings to fix these problems, and Ifju drew on his windsurfing passion to expand their work. His idea: Flexible sail-like wings made out of carbon fiber frames covered with latex skins. In theory, the greater flexibility of the surfaces would allow them to roll with wind gusts — more like birds than traditional planes.
“The general concept is a wing that has the biological semblance of a bat’s wing, with a skeleton and an extensible membrane covering it,” Ifju says.
The idea came to Ifju only months before the third International Micro Air Vehicle Competition in 1999, and at first it looked like a loser.
“We built dozens of models that didn’t fly well, or didn’t fly at all, in 1999,” Ifju says. “We didn’t know whether we were on the right path or not.”
Finally, by focusing on aligning the plane’s center of gravity just so, Ifju and his researchers produced a flying model. The researchers spent the next couple of weeks tweaking it, and UF won the third competition with a plane with a 12-inch wingspan, setting a new record in the process.
As intended, the design proved easy to test and modify. The results have been impressive. Despite facing competitors from the Georgia Institute of Technology and other top-flight engineering schools, UF has won every annual MAV competition since 1999. UF researchers have received more than $6 million in grants for MAV research, much of it tied to the flexible-wing technology. And faculty and graduate students have published dozens of academic papers on various aspects of the flexible-wing development.
“I still believe that our success is almost entirely dominated by the fact that we realized early on that you had to have robust construction,” Ifju says.
Also a big help: MAVs appeal greatly to undergraduate and graduate students. About a dozen graduate students and 30 undergraduates — a quarter of the undergraduates in the aerospace engineering department — are involved in some aspect of MAV research, says Rick Lind, associate professor of engineering and MAV researcher.
“The undergraduates like it because they don’t necessarily have the math skills yet, but they can build the airplanes,” he says. “The graduate students don’t want to do the hands-on work because it’s not going to get them their PhDs, but they need the airplanes to make a theoretical contribution.”
Design, Build, Fly
Haftka and Jenkins gradually became less involved with the MAV research as Ifju’s work intensified. This decade, Ifju and his students steadily produced smaller, more reliable planes, some with latex wings and some with bendable wings made completely of carbon fiber. They also crafted a customized computer design program Ifju named MAV Lab. “We put a lot of work into rapid prototyping technology,” Ifju says.
The program allows researchers to create three-dimensional virtual wings and flaps in as little as 15 minutes. With the touch of a button, researchers can send instructions based on their virtual concepts to a milling machine, which cuts a mold for epoxy-impregnated carbon fiber. Researchers assemble the surface, then use an oven to “cook” or heat it up to cure the epoxy overnight. With some additional labor — most fuselages continue to be built by hand — the plane can be ready to fly the next day. The bottom line: A design-build-fly timeline of 24 hours, ideal for rapid testing.
Other recent developments have helped. In 2001, stick-of-gum-sized lithium polymer batteries became available commercially for the first time, allowing researchers to replace old gas-fueled motors with electric motors. The extremely reliable batteries make repeated test flights easy. And where the old motors could run for less than five minutes, the new battery-powered motors can keep planes aloft for as long as 30 minutes.
Ifju’s team steadily shrank its planes, and UF won the most recent MAV competition in 2006 with a four-and-a-half-inch surveillance plane. The orange, blue and yellow palm-sized plane traveled 600 meters, or about a half-mile, to videotape a target.
As tiny as the plane was, its size may not be its most important virtue. Part of this year’s competition required entries to be compact. Using the all-carbon-fiber wings, the UF plane can be folded up and fit into a 1-by-3-inch tube slightly larger than a lipstick tube. That points up the latest MAV research: Researchers are less interested in making them smaller and more interested in making them compact, user-friendly and robust.
“It’s more about the applications these days,” Ifju says.
At a time when much larger surveillance drones are widely used in Iraq, Afghanistan and Israel, Ifju has a hand in several efforts that bode near-term real-world deployment of MAVs. A company called Applied Research Associates tapped his research to build a two-foot MAV called “TacMAV” that was tested in Iraq. His project for the U.S. Special Forces involves designing a MAV with carbon fiber bendable wings to fit into a uniform trouser pocket. In yet another effort, he is building a MAV that can piggyback on the U.S. Air Force’s 28,000-pound Massive Ordinance Airdrop bombs, then eject itself shortly before the bombs hit their target to conduct damage assessment.
“Right before this bomb hits, it spits out this little container that has a little parachute, which decelerates to some terminal velocity,” Ifju says. “This container opens up, our vehicle pops out, stabilizes itself, gets a GPS lock, then flies to where the bomb is supposed to hit and checks out the damage.”
Transformers
For such applications to work well, the planes need to do more than just fly. They also have to be able to fly on their own, or at least with as little assistance as possible from a human pilot. Much of the current research attacks this challenging problem. Miniature autopilot systems for traditional hobbyist planes are available commercially, but they are far too big and heavy for the smaller MAVs. And autopilot is only one aspect of autonomy. Planes also have to be able to carry and access information about their location, destination and mission, and to transmit and receive.
That's a tall order for a plane that weighs a few ounces.
"You have to have transceivers on board, GPS, accelerometers, gyroscopes, airspeed indicators, altimeters...," Ifju says. "It's like ca-ching, ka-ching, ka-ching, the weight budget keeps going up and up and up."
Even if the planes can carry all the hardware, they will still require smart programming to put it to use. Lind and his students devote much of their efforts to attacking this problem. One of his projects involves a vision algorithm intended to help the airplane discern features such as buildings, hills or bridges so that it can navigate around them. "We want to use that information to estimate path planning so, given some crude outline of a building, the plane knows to turn left for half a mile, then right for 300 meters, then maybe climb for 60 meters and so on," he says.
A Florida startup company, Prioria, has licensed Ifju's bendable wing technology and is designing a military MAV it expects to release for sale early next year. The company-designed autopilot aboard "Maveric" has obstacle avoidance as well as target-recognition technology also rooted in UF MAV research, says company president Brian da Frota. "The plane goes out and looks for interesting targets and then sends that information back to the ground," he says, adding that the company expects to produce between 25 and 50 Maverics in its first year of manufacturing.
Lind and doctoral student Mujahid Abdulrahim are also making MAVs more maneuverable by building airplanes that "morph," or change shape, dramatically during flight, transforming the planes' stability and agility. With the wings in the down position, the plane loses stability but becomes highly maneuverable. With the wings in the elbow-straight position, it glides well. And with the wings in the elbow-up position, it's highly controllable and easy to land.
"Now it's a question of, 'can the plane do a precise maneuver?," Lind says. "Instead of just flying in a field, can it fly into a window?," adding that he and his colleagues are also working on planes whose wings change shape on the horizontal axis, another approach that could aid maneuverability and endurance against turbulence.
Ironically, the next revolution in MAVs might not be in the air but on the ground. The military is very interested in planes that could fly to a location, then crawl along the ground. A just-announced $6 million Air Force program, Aerial Robotic Transformer, will soon accept applications for grants, and Lind and Ifju plan to submit proposals.
"They want an airplane where you can land it some place in the open, then crawl to a dark corner where the bad guys can't see it," Lind says.
Raphael Haftka
Distinguished Professor, Department of Mechanical and Aerospace Engineering
(352) 392-9595
haftka@ufl.edu
Peter Ifju
Associate Professor, Department of Mechanical and Aerospace Engineering
(352) 392-6744
ifju@ufl.edu
Dave Jenkins
Associate Engineer, Department of Mechanical and Aerospace Engineering
(352) 392-6105
davej@ufl.edu
Rick Lind
Assistant Professor, Department of Mechanical and Aerospace Engineering
(352) 392-6745
ricklind@ufl.edu
Related Web Sites:
http://mav.mae.ufl.edu/mav
http://mav.mae.ufl.edu/morph |