UF researchers are refining the process they invented for turning all kinds of plant material into the automotive fuel of the future.
By Joseph Kays
downloadable pdf
Lonnie Ingram looks at mountains of sugarcane waste in Belle Glade and sees ethanol. He looks at truckloads of orange pulp and peels in Orlando and sees ethanol. He looks at piles of yard waste at the Gainesville landfill and sees ethanol.
While farmers in Iowa promote corn as the raw material of choice for a new ethanol-based transportation economy that’s being touted by everyone from George W. Bush to Al Gore, Ingram and many others believe the one billion tons of inedible biomass generated in the United States annually — including 124 million tons in Florida — offer a more cost-effective, environmentally sensitive alternative known as cellulosic ethanol.
And Ingram is in a position to know. A distinguished professor of microbiology at UF and member of the National Academy of Sciences, he has spent the last two decades inventing and refining what many believe is the most promising approach yet to converting all that plant waste material into cellulosic ethanol.
The United States is already the world’s largest producer of ethanol, but the 5 billion gallons produced annually represents less than 4 percent of the 140 billion gallons of gasoline we use every year, and virtually all of it comes from corn.
Corn has been the predominant feedstock in the United States for decades because turning it into ethanol is easy. In a process akin to making moonshine, the starch in the corn is mixed with enzymes to separate out glucose which is fermented with yeast to make alcohol.
But corn is both environmentally and economically expensive because it requires a lot of energy to grow — think big diesel tractors and lots of fertilizer — and is also used for a lot of other things Americans enjoy, like soda and cereal. In fact, the U.S. Department of Energy estimates that producing more than about 15 billion gallons of corn ethanol a year would impact the price of all other corn-based products.
“The net positive energy from cellulosic energy has been estimated by the Department of Energy at about 85 percent, with 15 percent to grow crops, transport and produce,” Ingram says. “Corn is the exact opposite, 15 percent positive energy compared to 85 percent to grow the corn.”
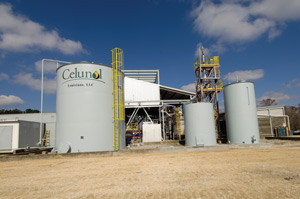 |
Celunol, which has research facilities at UF's Sid Martin Biotechnology Incubator, is constructing the nation's first cellulosic ethanol plant using Ingram's technology in Jennings, Louisiana. |
Cellulosic ethanol is chemically identical to corn ethanol and offers all of the same benefits — renewable, clean-burning — without the massive energy requirement and food competition. And Florida is the nation’s biomass giant.
“Florida produces more biomass per year than any other state in the country,” says Ingram, who also serves as director of UF’s Florida Center for Renewable Chemicals and Fuels. “We have a climate that allows things to grow year-round. Estimates are that we could make as much as 10 billion gallons of ethanol a year from biomass resources, and much of that would be from material that is currently going to landfills, like yard waste.”
But pine trees and orange peels don’t give up their sugars easily. The fibers that make up 80 percent of non-edible biomass are comprised of complex five- and six-carbon sugars, and there are no naturally occurring organisms like yeast that will convert these types of sugars to ethanol.
So 20 years ago Ingram and his colleagues genetically engineered the best traits of two common bacteria — E. coli and Zymomonas — to create a new organism that could perform a two-step process to first convert those complex sugars to acids and then convert the acids to ethanol.
That accomplishment earned Ingram and two colleagues the nation’s landmark 5 millionth patent in 1991. But after an elaborate ceremony in Washington where the Secretary of Commerce lauded their achievement, it was back to the laboratory for Ingram to figure out how to make the process economically feasible.
“We first developed an organism that would work,” Ingram says. “Since then, we have been evaluating the cost of the different components in the process and identifying the biological impediments to simplifying that process to reduce its cost.”
For example, Ingram says, the rich medium used to ferment the cellulose in the early experiments would have pushed the cost of the ethanol to more than $5 per gallon, including $4 just for the medium.
“We have now reduced that to a nickel or less per gallon,” Ingram says. “It was absolutely essential to do that in order to make this economically feasible.”
Another challenge was increasing the amount of ethanol the organisms produce.
Ingram says the early organisms produced around 4 percent ethanol, less than half that of corn.
“Now we’ve more than doubled the alcohol level that’s produced to about 9 percent,” Ingram says.
The researchers also have optimized the organisms so they can simultaneously ferment several types of sugars, increasing the yield and “getting the material in and out of the tank faster,” Ingram says.
All of these advances are important to the commercialization of cellulosic ethanol, Ingram says, because they impact the amount of raw material and the size of the plant needed to produce a given amount of fuel.
“If you double the ethanol concentration, then you can reduce the plant size by half,” he says.
“This is how basic science is commercialized,” he adds, drawing a parallel to Thomas Edison’s years of tinkering with the filament for the electric light bulb. “First you develop a process that will work at some level, then you refine it.”
Much of that work will now be done in two state-funded facilities, one on campus and one at a commercial site.
Earlier this year, the Legislature and Gov.
Charlie Crist authorized $20 million for UF to construct an ethanol demonstration plant that will produce 1 to 2 million gallons per year, enough to fuel most of UF’s fleet of vehicles. The university is currently seeking a partner to develop the plant.
UF also received a $4.5 million Florida Center of Excellence grant last year, part of which will be used to develop a small pilot plant in the Department of Agricultural and Biological Engineering. Researchers plan to use the pilot plant as a platform to accelerate successful commercialization of bioethanol. They will focus on streamlining production processes, testing the feasibility of various materials available in Florida as raw material, and demonstrating all the steps needed for commercial production.
Ingram, who sat next to President Bush during a February meeting at the White House on alternative energy, believes the country has finally reached a “tipping point” on energy.
“I believe there is a fuller recognition of the problems associated with our dependence on imported petroleum and, of course, concerns about climate change and the need to move to renewable energy sources,” he says.
Now everyone is jumping on the bandwagon. Earlier this year, the energy consulting firm Clean Edge Inc. reported that investment in U.S. biofuel companies grew from $800,000 in 2004 to $813 million in 2006.
Among the companies big venture capitalists are investing in is Celunol — a Massachusetts-based company that holds the exclusive license from UF to develop Ingram’s cellulosic ethanol technology. Celunol, which also has research facilities at UF’s Sid Martin Biotechnology Incubator, is constructing the nation’s first cellulosic ethanol plant using Ingram’s technology in Jennings, Louisiana. Celunol expects the plant — which will use the sugarcane waste known as bagasse as its raw material — to produce up to 1.4 million gallons of ethanol per year.
“It has become clear that we need to look to new feedstocks and technologies to increase the sources of supply of ethanol,” says Carlos Riva, Celunol’s president and CEO. “A successful demonstration in Jennings will mark the last major step before the full-scale commercialization of this exciting new technology can begin.”
In March, the U.S. Department of Energy awarded Celunol $5.3 million — the largest of five research grants totaling $23 million related to cellulosic ethanol fermentation process technology.
“Ultimately, success in producing inexpensive cellulosic ethanol could be a key to eliminating our nation’s addiction to oil,” U.S. Secretary of Energy Samuel Bodman said in a statement in February. “By relying on American ingenuity and on American farmers for fuel, we will enhance our nation’s energy and economic security.”
Lonnie Ingram
Distinguished Professor, Department of Microbiology and Cell Science
(352) 392-8176
ingram@ufl.edu
Related Web site:
http://fcrc.ifas.ufl.edu
Breeding Trees to Facilitate Ethanol
In a UF greenhouse, researchers Matias Kirst, Gary Peter and John Davis discuss the growth of thousands of black cottonwood saplings to test genetic variation within the species. |
UF researchers, in conjunction with 33 scientific institutions worldwide, have mapped out the genome of the black cottonwood tree, a prime candidate for use in new “biomass” fuel production methods.
The research identifies genes that can be specifically selected through traditional plant breeding to produce trees with the perfect qualities for efficient conversion into biomass fuel.
The genomic research revealed 93 genes that help control the production of cell wall substances. By breeding trees with just the right variation of these genes, researchers can produce the ideal energy cash crop that could help replace as much as half of the oil imported into the United States.
“This is a wild tree, and there’s enough genetic variation already out there for us to get the plant we want without direct genetic manipulation,” says John Mark Davis, one of three UF researchers who collaborated on the project.
In ideal environments, the trees already grow rapidly, as much as 12 feet in a year, and can reach maturity in as little as four years. But the genome could also mean breeding trees that respond well to less-than- ideal environments. The result could be a new type of crop that could be grown throughout Midwestern and Pacific Northwest states, says UF researcher Matias Kirst.
Of course, vast farms of the black cottonwood would come with another advantage other than cleaner-burning, cheaper fuel — the trees, like all plants, absorb the most significant greenhouse gas, carbon dioxide. They then store the carbon in their stems, roots and the soil.
“Basically, you would have a fuel source for our cars that, in the big picture, could help capture almost as much carbon dioxide as it produces,” said UF researcher Gary Peter. “That would go a long way in slowing the biggest driver of global warming.”
The effort to sequence the black cottonwood’s genome was funded by the U.S. Department of Energy and included institutions such as Oak Ridge National Laboratory, the University of British Columbia and Ghent University in Belgium.
This is only the third plant genome to be sequenced, and it contains nearly four times more genetic information than that of either rice or Arabidopsis thaliana, a flowering weed. More than 45,000 genes were identified — that’s twice the number identified in the human genome, which is six times larger than that of the cottonwood.
While computers have helped identify which genes may be responsible for certain characteristics, trees with those specific genes must still be grown, tested and harvested. Peter, Davis and Kirst are growing thousands of trees with hundreds of different genetic variations in an environmentally controlled greenhouse.
John Mark Davis, jmdavis@ufl.edu
Gary Frank Peter, gfpeter@ufl.edu
Matias Kirst, mkirst@ufl.edu
Stu Hutson
|